|
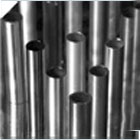 |
Electro Circuit Treatments offers its customers a variety of quality plated finishes for electronic Circuit. Each customer requirement is carefully analyzed for optimum results. Process planning for successful plating of intricate parts begins before the work reaches the production floor. Proper electro placements, configurations, and unique designs are used, as are in-process quality audits and electro-chemical formulations for quality results. Several methods of masking are also available for selective plating applications. It is through these efforts that Electro Circuit Treatments consistently maintains the high quality its customers demand.
The plated finishes listed below are offered in electro plating over the following base material: aluminum alloys, nickel, steel, stainless steel, copper, and copper based alloys.
Electro Circuit Treatments is currently serving the aerospace, electronics, medical, automotive and commercial industries with plated finishes. Whether you require plating on chem-mill sheets, opto devices, delicate connectors, or need intricate maskings or high cosmetic standards, Electro Circuit Treatments welcomes the opportunity to deliver your product on time with competitive prices and consistent high quality.
Gold plating is intended for electrical applications, and where good corrosion resistance, excellent solderability, or high tarnish resistance is need. It also has uses in many other applications. The color is yellow to orange depending on the proprietary process used, and will range from a matte to bright finish depending on the base metal and purity of deposit. It has low contact resistance, and is a good conductor.
Silver plating intended for engineering purposes is usually employed for solderable surfaces, electrical contact characteristics, high electrical and thermal conductivity, thermocompression bonding, wear resistance of load-bearing surfaces, and spectral reflectivity.
Nickel plating intended for corrosion protection is used to protect iron, copper, or zinc alloys against corrosive attack in rural, industrial or marine atmospheres depending upon the thickness of the nickel deposit or is used as an undercoat for chromium or one of the precious metals. Also used for decorative purposes.
Nickel plating intended for engineering purposes is used for wear resistance, abrasion resistance and such incidental corrosion protection of parts as the specified thickness of the nickel plating may afford. Heavy deposits of the plating, especially when the Watts bath process is employed, may be used for build up of worn or undersized parts, or for salvage purposes, and to provide protection against corrosive chemical environments
Electroless Nickel plating is primarily used to provide hard, ductile, wear-resistant, and corrosion-resistant surfaces for operation in service up to 1000°F (40°C) and to provide uniform build-up on complex shapes. Similar to stainless steel in color.
Tin plating intended for engineering purposes is used for corrosion protection, to facilitate soldering, to improve antigalling characteristics, and as a stop-off barrier in the nitriding of high-strength steels. Color is gray-white, matte to bright in appearance depending on the process used. Soft and very ductile, not good for low temperature applications.
Copper plating can be used as a heat treatment stop-off shield, carburizing or decarburizing shield, an undercoat for nickel and other metals, or to prevent base metal migration into a tin layer. Copper in color and matte to a very shiny finish, it has good corrosion resistance when used as an undercoat. Several copper processes are available, each designed for a specific purpose: Bright, to eliminate buffing; High Speed, for electroforming; Fine Grain, to prevent case hardening, etc.
Tin/Lead Alloy plating is primarily used as a coating for corrosion protection, and as a base for soldering. Color is gray-white, matte to bright in appearance depending on the process used.
|
|